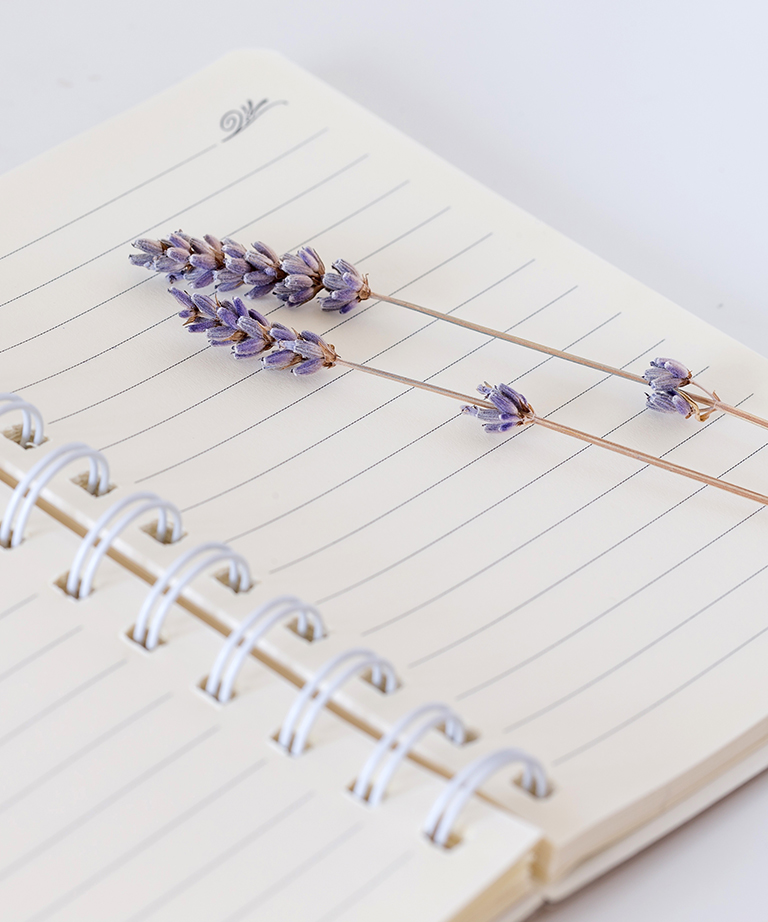
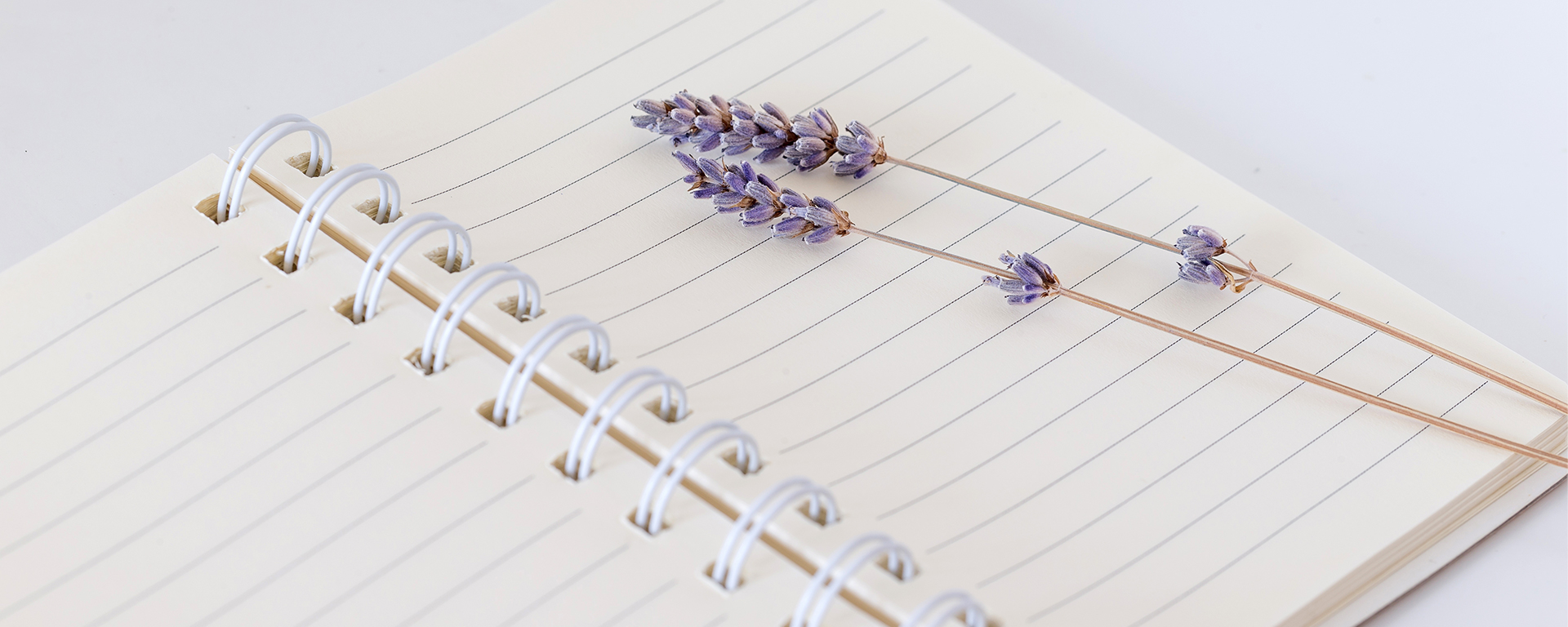
QUALITY AGREEMENT
QUALITY AGREEMENT
1. General
Mann & Schröder GmbH (hereinafter referred to as “M&S”) expects optimal quality from its suppliers at an economically justifiable cost. Optimal quality is to be understood not as meaning the highest possible quality of a product, but instead as the fulfilment of all defined requirements taking into account the “no error” philosophy. M&S has developed an effective quality management system in order to achieve this goal. The contractual partners are of the opinion that high, optimised quality and reliability can only be achieved when a business relationship has at its foundation a partnership collaboration in the production of the products, the process inspections and the applied inspection methods.
2. Scope
This quality agreement for deliveries to M&S (hereinafter referred to as “M&S QA”) is obligatory for all suppliers of primary and secondary packaging materials, raw materials, sub-contracted production and additional purchases of finished products. The M&S QA applies in respect of M&S and all companies associated with M&S. (see Article 15 of the German Stock Corporation Act). The M&S QA forms part of the contractual relationship and, along with the supply agreement, the M&S Conditions of Purchasing and Ordering and any further potential agreements concluded with the supplier, constitutes the legal framework of the business relationship with M&S, whereby the ranking of the individual components of the contractual relationship is determined in the supplier agreement.
The most current version of the M&S QA applies in each case with such being available to view at any time on the M&S website. Amendments to our Quality Agreement also apply as part of an existing supply agreement. Our suppliers undertake accordingly to keep themselves regularly informed of the current version of our Quality Agreement. Corresponding amendments to our Quality Agreement are made in the exercise of the service determination right agreed with our supplier at our equitable discretion. Should a supplier believe an amendment to our Quality Agreement is inequitable as
part of an existing supply agreement, it has the right to raise objections within four weeks following the publication of the amended version. Where such objections are not raised, the amended version is deemed to be accepted by the supplier, too.
3. Quality
3.1 The supplier is responsible for ensuring that the delivered products comply in full with the agreed specifications of M&S (in particular material specification, raw material specification, technical drawing, specification sheet etc.). These specifications each form part of the M&S order. Amendments require prior written confirmation by M&S. Deliveries which deviate from the M&S specifications are not permitted.
3.2 The supplier shall ensure that the product complies with legal provisions, guidelines and directives and standards. Where applicable, the supplier shall in particular ensure compliance with the requirements of the Regulation (EC) 1223/2009 (EU Cosmetic Products Regulation) and all related provisions. The supplier shall observe these principles and use them as a foundation for deliveries to it made by third parties for the product.
3.3 M&S undertakes to inform its suppliers of all known and determined requirements of the product. The supplier shall carefully check this information. Inconsistencies, in particular contradictions to or deviations from the “Principles of Good Production Practice” within the meaning of Article 8 of the EU Cosmetic Products Regulation and DIN EN ISO 22716 are to be stated. Where inconsistencies occur, it is the responsibility of the supplier to clarify matters with M&S. This is to happen before materials/raw materials are produced and/or delivered.
3.4 It should be guaranteed that the product complies with the corresponding standards throughout the planned market placement process of the product. The same applies where the product is inspected by test institutes. In this respect it should also be guaranteed that the product shall take into account the amended/increased quality and test requirements.
4. Prototypes, initial samples and series delivery
4.1 supplier in laboratory conditions or, when using packaging materials, the existing products situated with the supplier are to be presented with the corresponding documentation (e.g. M&S technical drawing (purchasing department) or to a specified third party for testing. Where M&S or the third party selects a prototype presented by the supplier, the supplier shall immediately make available to M&S or the third party the weighted INCI, the specification, any advertising messages, mandatory labelling, warning and operating information (such as information on minimum durability) as well as the documentation within the meaning of Clause 8 of this agreement in respect of this product. The supplier shall also ensure that the initial sample and the products produced in a series display in every respect (and in particular regarding quality) the characteristics of the prototype products.
Initial samples are products, raw materials and materials which are produced in full with series-type equipment and under series-type conditions. Initial samples are to be presented to M&S (Purchasing, Technical Marketing and Quality Assurance departments) along with a complete initial sample test report. The initial sample test report is to be presented with the associated labelled samples (amount as per the sample order or as per agreement with the initial sample test centre) to the departments stated above. Parts for multistage tools are to be tested, labelled and separately logged per form nest. The initial sample test report is to be attached to the part history documentation. The part history documentation records fully and clearly all amendments to a part, the date for the presentation of the sample and the first series delivery.
The initial sample test report shall contain the following for each product group:
- A measurement log with a target/actual comparison for all quality benchmarks. Process capability proofs are to be made for important benchmarks (control measurements in the drawing) and attached to the initial sample test report.
- The materials test is carried out by means of a target/actual comparison as per the drawing information.
- The following proofs are to be attached:
- Safety information sheet as per the REACH Regulation (EC) no. 1907/2006 with comment on the reliability of the intended use (e.g. use in cosmetic products)
- Specification of the packaging material used and, where needed, proof of biocompatibility
- Analysis certificate, specification, MSDS, product/regulatory dossier/information on raw materials; additional documentation is made available to M&S where needed
- Delivered product batch
- Any functionality test carried out should include a target/actual comparison as per the drawing information and specification
An initial sample is always needed:
- For new or amended products/processes
- Before beginning a series of products made from new materials or with new tools
- Before beginning a series of products from new sub-suppliers
- When using relocated tools or shifting production facilities
- When production ceased for a period of one year or more
Where any amendments are made (e.g. product, process, tool, material) a sample is to be made of the amended characteristics. Reference is to be made to the previous initial sample test report.
Series delivery can only be made once the initial sample has been approved in writing. Where this is not possible due to time constraints, the supplier shall obtain special approval from M&S. The supplier shall store all initial samples during a period of time which corresponds to the planned minimum durability of the first sample product/materials/raw materials and which shall not, however, be less than three years as calculated from the time of the first sample. Storage shall be carried out appropriately and professionally. During this time the supplier shall ensure M&S has access to the initial sample at any time. Where M&S is supplied with cosmetic products, the requisite documentation for complying with the EU Cosmetic Products Regulation are to be made available to M&S. This is particularly relevant in respect of assessing safety, the product information file and the weighted INCI. Insofar as M&S appears to be the distributing company, notification shall be made by M&S.
4.2 Insofar as the supplier delivers an end product to M&S which is to be brought to market by M&S without amendment, the supplier shall arrange to have a product sample from the first produced batch tested at its own cost by an independent and recognised testing institute to be agreed on with M&S and in particular in respect of contained substances, marketability, efficiency, compliance with requirements of consumer testing facilities (Stiftung Warentest und Ökotest GmbH) as well as other criteria relevant to the market and/or agreement (in particular the production specifications agreed in the agreement with M&S). The product is to be such that it achieves optimal results in tests carried out by Stiftung Warentest und Ökotest and other test institutes.
5. Fundamental requirements of the quality management system of the supplier
5.1 The supplier undertakes to maintain and sustain a quality management system which comprehensively regulates the processes relevant for ensuring quality. The quality management system shall at a minimum meet the requirements set by DIN EN ISO 9001:2008. M&S is to be informed of any amendment to the quality management system.
5.2 The supplier shall, at a minimum, maintain and sustain a quality management system in accordance with DIN EN ISO 9001:2008 for identifying, amending, collating, archiving and distributing quality record data. The system is to ensure that sufficient records are made for each delivery to M&S. This shall include records made by sub-suppliers. In the case of activities subject to documentation requirements, the supplier undertakes to fully document the quality assurance measures and corresponding results taken by it or its sub-suppliers and to maintain such information for a period of at least ten years following the delivery of the last batch.
5.3 The supplier shall ensure that only materials/substances and processes are used which are permitted in the specifications. In this respect consideration is to be had of all legal and safety conditions for unrestricted, permitted, poisonous, dangerous and banned substances. Further, the regulations on environment, electricity and electromagnetic fields applicable in the country of production and receipt are to be met.
5.4 M&S reserves the right to impose additional special product-specific quality assurance measures on the supplier where critical materials are being used.
5.5 Where a supplier is not certified to DIN EN ISO 9001:2008, M&S and the supplier shall decide in a separate agreement whether and by when the supplier is to obtain a corresponding certification. Further, such a supplier shall also be accordingly subject to the provisions in this Quality Agreement. The supplier undertakes to make M&S expressly aware of it not complying with the obligations under this quality agreement.
6. Inspection of incoming goods by the supplier
6.1. Principle
The supplier shall carry out an appropriate incoming goods inspection on all raw and packaging materials in respect of identity, quality and quantity.
The supplier undertakes to retain samples of each batch of products, any raw materials and packaging used and to store them properly. The retained samples are to be stored in such a way so as to exclude any chemical or biological changes. The following periods of storage apply to retained samples:
Raw materials and the respective analysis certificate of the raw material supplier: At least one year from delivery.
Retained samples of produced products: At least one year following the expiration of the ‘best before’ date of each product.
On request by M&S the supplier undertakes to hand over to M&S the retained samples and analysis certificates so an inspection can be made.
6.2 Raw materials
An identity test shall be carried out on the raw materials used in production before each delivered batch is used.
6.3 Packaging materials
Further, tests are performed on a sample basis on all deliveries of packaging materials in respect of colour, form, printing, functionality, safety and the amount delivered. Comparative samples are made available to M&S in advance.
6.4 Minimum requirement
The above tests are the minimum requirement imposed by M&S on suppliers. The supplier can carry out additional tests at its own discretion.
Where one of the required tests cannot be carried out by the supplier, M&S is to be consulted as to alternative courses of action.
M&S reserves the right to carry out external tests on a sample basis a maximum of once a year. The payment of related costs is borne by the supplier.
7. Supplier responsibility
Irrespective of the requirements imposed on the supplier by M&S, it is the sole responsibility of the supplier to have installed a sufficiently functioning quality assurance system. Audits and checks by M&S of the supplier do not release the supplier from its sole responsibility to check the functionality of its quality assurance system and the processes managed by it and thereby to guarantee that the prescribed processes are complied with and are also appropriate.
8. Documentation
8.1 The supplier shall ensure that documentation which is of significance for the quality of the delivered products are available at each place of work. This includes, for example, drawings, specifications, production and test instructions. This documentation is to be checked for accuracy and compliance with the requirements of M&S and subsequently approved.
8.2 The supplier shall ensure the quality of the products during the product creation phase and in the case of any amendments by demonstrably implementing QM methods in an effective way. This includes documents, test reports etc.
8.3 In addition, the supplier is to list all production and test steps in the internal working papers (QM plan, production quality planning) to be kept by it. Benchmarks to be monitored are to be specified and the type of monitoring shall be stated. The supplier shall provide proof of the control and functionality of processes for all important benchmarks (control measurements, characteristics) by recording the measurement data and its statistical treatment. The supplier shall statistically check and document these benchmarks during the production process.
In the case of series deliveries, acceptance test reports (DIN EN 10204 3.1B) and the safety information sheet as per the REACH Regulation (EC) no. 1907/2006 are to be kept by the supplier and made available to M&S on request. The supplier undertakes to create a retained sample for any product batches delivered. Such samples shall be kept for a minimum of three years.
9. Labelling and traceability
9.1 Systematic labelling of products, materials and raw materials makes it possible to ascertain the test status and the identification of the products, materials and raw materials delivered. This labelling and the accompanying documentation makes it possible to trace the products, materials and raw materials (including insofar as they are received by sub-suppliers). The supplier shall introduce and maintain a system for correctly identifying its products as well as their storage (FIFO principle), packaging and shipping. The system is to ensure that mix ups of or damage or impairment to parts is avoided. In the case of the first three series deliveries following an amendment, the analysis certificates and the current state of the amendment (E index) are to be labelled in case no article number has been issued. M&S shall determine on an individual basis whether further deliveries are to be labelled. Sample deliveries are to be clearly labelled as such. The recipient of the sample delivery is to be stated (name and department).
10. Test equipment/monitoring of test apparatus
The suppler shall have ready for the purpose of use corresponding measuring tools and test equipment which it needs for testing the M&S specifications throughout the series. The supplier shall label all test apparatus and equipment which could impact the quality of the product. The test apparatus is to be calibrated and adjusted before use in determined test intervals. The calibration status must be visible on the measurement apparatus and/or records are to be produced and kept regarding calibration. The capability of measuring apparatus is to be evidenced in the case of critical benchmarks. Measuring apparatus for weight control applications are to be calibrated in line with the applicable legal provisions.
11. REACH
The supplier undertakes to immediately and free of charge make available all information, documents and papers required by M&S to fulfil its duties and responsibilities under the REACH Regulation (EC) no. 1907/2006. Further, the supplier shall make available within a week of a request by M&S significant information which provides that the substances used in its products are safe for use by M&S, in particular in respect of use in cosmetic products.
Substances of very high concern (SVHC) - Obligations pursuant to Article 33 of the REACH Regulation (EC) 1907/2006:
Pursuant to Article 33 of the REACH Regulation (EC) 1907/2006 it must be ensured that sufficient information exists on substances of very high concern contained within articles along the chain of delivery so as to ensure that such articles are used safely.
The producer and supplier of articles which contain substances of very high concern (see the website of the European Chemicals Agency (ECHA) for more information - http://echa.europa.eu) in a concentration exceeding 0.1 per cent by weight, must make available all available information directly and without prompt. The supplier of an article shall also inform Mann & Schröder GmbH when a product does not contain any substances contained on the list of substances of very high concern (“Negative Information”). This information on SVHC is to be made available without request in accordance with the obligation under Article 33(1) along with the CAS number, the EINECS number, the name of the substance and the content of the SVHC. This obligation applies irrespective of weight. The obligation to make available existing information on SVHC (subsequently implemented in Annex XIV of the Regulation (EC) 1907/2006) refers to the packaging material used for cosmetic products (= article). To this end the supplier of the article shall send to Mann & Schröder GmbH an “analysis certificate per article” for each article delivery which contains information on the content of the SVHC.
So as to fulfil the REACH obligation the supplier of an article is to always observe the list of SVHC as this is continually updated and expanded. Further, account should be taken of the “Guidance on requirements for substances in articles”. With each addition to the list of substances of very high concern the supplier of the article shall send to Mann & Schröder GmbH without request information on the content of this new SVHC included on the list.
Further, it shall be ensured that the packaging material which comes in indirect or direct contact with the bulk or formation conforms to food standards. This is to be evidenced with corresponding documentation upon a request by M&S.
Where sufficient information on the SVHC (presence, content etc.) is not made available to Mann & Schröder GmbH by the supplier of the article, Mann & Schröder GmbH reserves the right to commission chemical analyses with account taken of the current list of SVHC. The costs of these analyses shall be borne by the supplier.
12. Audits and control rights
12.1 The supplier permits M&S and, insofar as desired by M&S, the customers of M&S to carry out process, procedure and system audits. The costs of the audits (including the auditors’ travel costs) are borne by the supplier insofar as they do not exceed a reasonable amount. M&S determines the content and scope of the audits. The audits are carried out subject to prior agreement on timing. The supplier undertakes to make possible an audit at the latest within 48 hours of the occurrence of a quality-related problem. M&S is entitled, as part of the audit, to an unrestricted right to information in respect of the goods to be produced for M&S as well as the equipment of the supplier needed for production.
12.2 The determinations made as part of the audit of the supplier, and in particular the classification of the supplier, is based on the supplier assessment by M&S which is made at the sole discretion of M&S.
12.3 M&S has the right to test, either itself or through an agent and without prior notice, compliance with M&S QA obligations during the regular working hours of the supplier’s production sites provided such sites either produce or store products destined for M&S. The supplier and M&S shall reserve corresponding authority for potential sub-suppliers.
12.4 Further, the supplier shall grant M&S as part of the EU Cosmetic Products Regulation a corresponding right of access and inspection in respect of the documents listed in the EU Cosmetic Products Regulation for a period of ten years (beginning with the time at which the last batch is brought to market).
12.5 M&S is entitled to have the corresponding audits and checks carried out by a recognised testing institute at the cost of the supplier. The supplier has the right to suggest the testing institute in question or to name a corresponding testing institute. Where the supplier and M&S cannot come to an agreement on whether the testing institute is independent and recognised, M&S has the right to decide on the testing institute.
12.6 M&S shall inform the supplier of the result of each audit. Where M&S is of the opinion that measures need to be taken to secure or improve product quality, the supplier immediately undertakes to produce a corresponding plan of measures, implement such immediately and to inform M&S accordingly.
13. Amendments to the supplier’s quality management system
Amendments to the quality management system of the supplier are to be notified to M&S (“Sales” department and the relevant contact for quality issues) within 48 hours of the amendment taking place. Amendments resulting in a qualitative deterioration in the quality management system are not permitted and may only be made with the agreement of M&S.
14. Service quality/safety
14.1 The supplier shall comply with delivery obligations in respect of quality and delivery reliability. It shall ensure that series products are produced, checked and documented with consideration of the requirements and that they comply with the M&S specifications. Delivery reliability and extra freight costs for M&S are to be monitored and evaluated. M&S is to be immediately informed in the case of non-compliance.
The costs of extra journeys caused by the supplier are to be borne by the supplier. At the same time suggestions for improvements, such as to how extra journeys can be avoided in future and delivery reliability can be increased, are to be submitted to M&S.
14.2 The supplier shall ensure, as part of its transport safety obligation, that its products are marked with any necessary safety messages. M&S is to be immediately informed of any amendments to safety information sheets. Further, updated safety information sheets are to be made immediately available to M&S.
15. Exit inspection and approval
15.1. Quality tests, inspections
Before sending products to M&S it must be ensured that the scope of tests and inspections includes at the least:
- The type and quantity of the products.
- All packaging materials used
- Check of compliance with the given weight control as per the specifications
- Packaging material and content test during current production as per requirements
- Microbiological test of each batch of finished products as per the specifications
15.2. Approval
The supplier is responsible for checking and approving the packaging material, raw materials, intermediary and end products used at its own authority.
Approval can only be made when all required checks are carried out and no deviations from the requirements are ascertained.
The supplier shall immediately send to M&S quality assurance the number of samples given in Annex 2 of the “Supply Agreement for Cosmetic Products” for each approved batch of finished products and also written evidence of the approval of this batch.
15.3 Incoming inspection by M&S
As part of its exit inspection the supplier also carries out the incoming inspection for M&S on the basis of an agency agreement (Article 377 of the German Commercial Code). The supplier undertakes to pay M&S damages for any erroneous inspections.
16. Deviations in quality
16.1 The supplier undertakes to notify M&S within 24 hours of the onset of any circumstances which could have an impact on the characteristics of the products which have been ordered. Any amendments to the product characteristics are to be carried out in principle as per Clause 4. Where the amendment is only temporary, e.g. defective production of a batch, a special written approval is needed from M&S (responsible party: quality management officer (QMO)). Affected batches may only be sent to M&S once special approval is granted in writing. The affected batches are to be labelled with the words “Special Approval” on delivery. The suppler shall inform M&S (purchasers and QMO) within 24 hours following the occurrence of existing or potential problems insofar as they impact on the quality or reliability of the products which have been delivered or pose a risk to future deliveries.
Where M&S ascertains that products, materials or raw materials of the delivered by the supplier deviate from the specification, these defects will be communicated to the supplier (Complaint report with blocking or claim). If the supplier is at fault for the deviation, M&S shall charge the supplier EUR 100.00 for each item delivered for the purposes of producing a test report to be used to enforce any defect claims. The supplier undertakes to immediately take any corrective measures and to maintain the supply of materials and raw materials. Where there is time pressure owing to deadlines, the supplier shall immediately make available corresponding personnel for sorting, reworking or replacing without defects any defective products. Where return deliveries are required, the supplier undertakes to collect the goods at its own cost within two working days. A debit notice, which is offset accordingly in the case of a new delivery, is automatically issued. Any implemented corrective measures are to be communicated by means of an 8D report to the issuer of the complaint report within a reasonable period of time. The efficiency of such measures is to be checked for future production.
17. Duration and validity
The M&S QA applies for the duration of the contractual relationship between the supplier and M&S.
18. Confidentiality clause
18.1 M&S undertakes to keep any delivered information confidential. However, M&S is authorised to use such information for registration, applications and for presentation to the relevant authorities. In individual cases such information may have to be made available to our trading partners. In such a case the supplier shall be informed.
18.2 M&S and the supplier undertake to treat confidentially all information of which they become aware as part of the audit in line with the confidentiality agreement to be agreed separately. The supplier may conclude confidentiality agreements with the customers of M&S in respect of all of the information concerning the audit.
19. Other provisions
If individual conditions of this M&S QA in whole or in part are or become invalid or if this M&S QA features a loophole, the validity of the remaining conditions shall not be affected by this. To replace the invalid provision, such a valid provision shall be agreed
as corresponds with the meaning and purpose of the invalid provision. In the event of a loophole, a provision shall be agreed that corresponds to that which would have been agreed in accordance with the sense and purpose of the remainder of this agreement if the matter had been considered at the outset.